Modular Cleanrooms: Enhancing Quality Control Across Industries
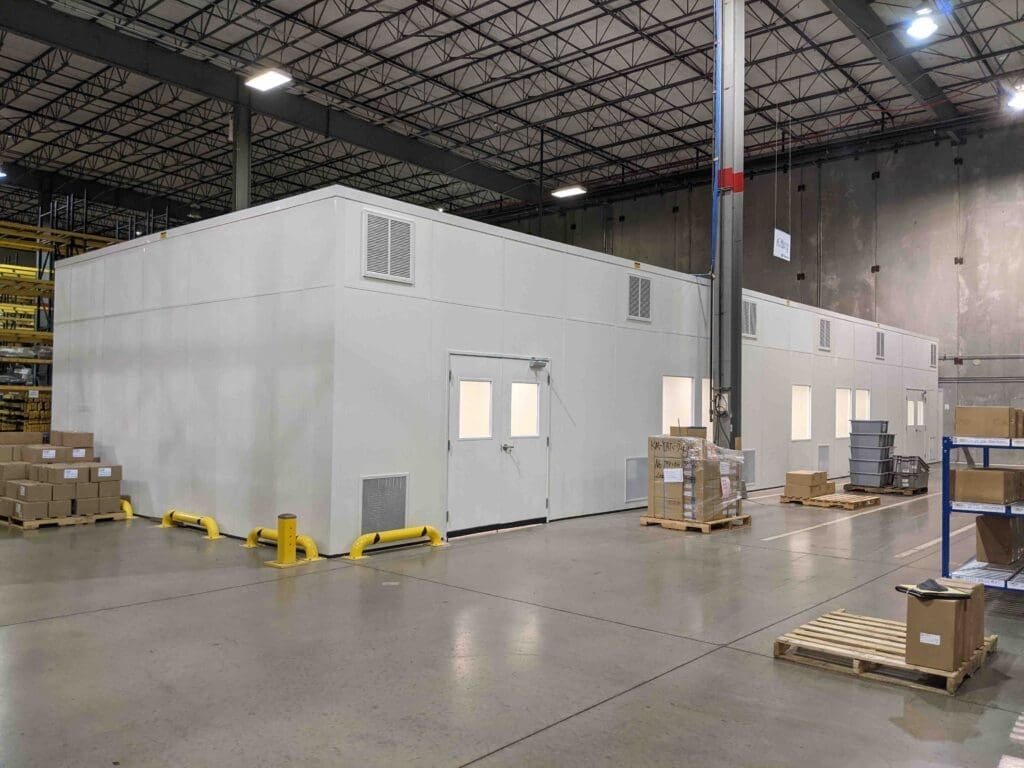
In today’s world of rapid innovation and stringent regulatory requirements, the need for controlled environments has never been more critical. Cleanrooms, which provide a contaminant-free space for various processes, have become crucial in many sectors. Modular cleanrooms stand out for their flexibility, efficiency, and enhanced quality control. This blog post delves into the advantages of modular cleanrooms, their diverse applications, and the industries that benefit most from these cutting-edge spaces.
What is a Cleanroom?
A cleanroom is a controlled environment designed to maintain low levels of particulates, such as dust, airborne organisms, or vaporized particles. The air quality in a cleanroom is typically measured by the number of particles per cubic meter at a specified particle size. Cleanrooms are essential in various industries, including pharmaceuticals, biotechnology, semiconductor manufacturing, and aerospace, where even the smallest contamination can compromise product quality and safety.
Types of Cleanrooms
Cleanrooms can be classified based on their cleanliness levels, measured by the concentration of particles per cubic meter. The most common classification standards are provided by the International Organization for Standardization (ISO) and the Federal Standard 209E (FED-STD-209E). Here, we will focus on the ISO classifications, which range from ISO 1 to ISO 9.
1. ISO 1 to ISO 3 Cleanrooms:
-These are the cleanest environments, with the fewest allowable particles. ISO 1 cleanrooms have fewer than 10 particles per cubic meter.
-Used in industries like semiconductor manufacturing and nanotechnology.
2. ISO 4 to ISO 5 Cleanrooms:
-These have a higher particle count than ISO 1-3 but are still extremely clean environments. ISO 5 allows up to 3,520 particles per cubic meter.
-Common in pharmaceutical manufacturing and critical medical device production.
3. ISO 6 to ISO 9 Cleanrooms:
-These have progressively higher particle counts, with ISO 9 being the least strict, allowing up to 35,200,000 particles per cubic meter.
-Used in less sensitive manufacturing processes where a controlled environment is still necessary.
How Cleanrooms Work
Cleanrooms function by controlling the following parameters:
1. Airflow and Filtration:
-High-Efficiency Particulate Air (HEPA) or Ultra-Low Penetration Air (ULPA) filters are used to trap particles.
-Air is typically recirculated through these filters to maintain a clean environment
2. Environmental Controls:
-Temperature, humidity, and pressure are carefully regulated.
-Positive pressure is often maintained to prevent the ingress of contaminated air from adjacent areas.
3. Personnel and Equipment:
-Strict protocols are in place for personnel entering and exiting the cleanroom, including the use of gowns, gloves, and masks.
-Equipment used within cleanrooms is designed to emit minimal particles and is often subject to rigorous cleaning and maintenance schedules.
4. Material Flow:
-The movement of materials in and out of the cleanroom is controlled to prevent contamination.
-Often, airlocks or pass-through chambers are used to transfer materials while maintaining the integrity of the cleanroom environment.
The Benefits of Modular Cleanrooms
1. Enhanced Quality Control: Modular cleanrooms provide superior quality control due to their construction in a controlled factory environment. This process ensures consistent adherence to stringent quality standards, minimizing the risk of contamination and ensuring a high level of precision.
2. Flexibility and Customization: They can be tailored to meet specific requirements, whether it’s size, shape, or cleanliness level. This adaptability allows for easy expansion or reconfiguration as needs evolve, making them suitable for a wide range of applications.
3. Rapid Installation: A-WALL’s cleanrooms are prefabricated off-site, leading to a significantly shorter installation time compared to traditional cleanrooms. The quick assembly process minimizes downtime, allowing businesses to commence operations sooner.
4. Cost Efficiency: The efficient construction process of modular cleanrooms often results in cost savings. Lower labor costs, reduced material waste, and shorter project timelines contribute to a more economical solution compared to conventional construction methods.
Applications of Modular Cleanrooms
Modular cleanrooms are utilized in various applications where controlling environmental factors such as temperature, humidity, and particulate levels is essential. Key applications include:
1. Pharmaceutical Manufacturing: Pharmaceutical production demands stringent control of environmental conditions to prevent contamination. Modular cleanrooms provide the ideal setting for manufacturing medications, ensuring compliance with regulatory standards.
2. Biotechnology and Life Sciences: In biotechnology and life sciences, maintaining a contaminant-free environment is crucial for research and the development of biological products. Modular cleanrooms offer the precise control needed for successful biotechnological research and product development.
3. Electronics and Semiconductor Production: The manufacturing of semiconductors and other electronic components requires ultra-low levels of particulate matter. Modular cleanrooms provide the necessary conditions to ensure the integrity and performance of these sensitive products.
4. Aerospace and Defense: The aerospace and defense industries require clean environments for the assembly and testing of components and systems. Modular cleanrooms ensure these parts meet the highest quality standards, supporting the stringent requirements of these sectors.
5. Food and Beverage Processing: Certain processes in the food and beverage industry necessitate contamination-free environments to guarantee product safety and quality. Modular cleanrooms are employed to maintain hygiene and comply with health regulations.
Industries Benefiting from Modular Cleanrooms
The versatility of modular cleanrooms makes them valuable across a broad spectrum of industries, including:
1. Healthcare and Medical: Health centers and medical facilities use modular cleanrooms for sterile environments needed in operating rooms, pharmacies, and laboratories.
2. Advanced Manufacturing: Beyond pharmaceuticals and electronics, sectors such as automotive and cosmetics also benefit from the controlled conditions provided by modular cleanrooms.
3. Research and Development: Academic and private research institutions utilize modular cleanrooms for various scientific studies and product development activities.
4. Environmental and Analytical Testing: Organizations conducting environmental and analytical testing require contamination-free spaces to ensure accurate results, making modular cleanrooms an essential asset.
Conclusion
Modular cleanrooms are revolutionizing the field of controlled environments. Their enhanced quality control, flexibility, rapid installation, and cost efficiency make them an attractive solution for numerous applications. As industries continue to evolve and the demand for contaminant-free spaces grows, modular cleanrooms are set to play an increasingly vital role in ensuring product quality and operational efficiency. Whether in pharmaceuticals, biotechnology, electronics, or beyond, the benefits of modular cleanrooms are clear, making them a wise investment for any industry requiring stringent environmental control.
Manufactured by Warwick Products.
5350 Tradex Parkway
Cleveland, Ohio 44102
Phone - 216-252-9292 | 800-345-4400
FAX - 216-889-1263 | 888-432-9274
E-mail: info@a-wall.com
Privacy Policy